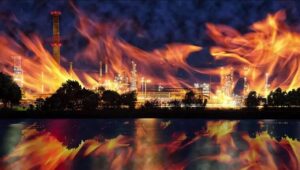
Transforming safety: Advanced Photonics Australia introduces the next generation of linear heat detection
Experience advanced linear heat detection with APSensing’s N45-Series. Elevate safety in industrial settings with precision fire monitoring.
Identifying abnormal heat patterns early can mean the difference between a near miss and a catastrophic fire.
Advanced Photonics Australia brings practical engineering expertise to the forefront. Harnessing cutting-edge photonics technology, we tackle each unique challenge head-on using Distributed Temperature Sensing (DTS).
This advanced technology, an evolution of Linear Heat Detection, enables rapid fire detection across vast distances with pinpoint accuracy.
Fires in the mining industry can result in millions of dollars of damages and present risk to lives. This highlights the critical need for early detection technology that can withstand corrosive environments without any operational interference.
Photovoltaic (PV) systems can generate powerful sources of heat. These high temperatures can lead to electrical fires and safety risks. Our cutting-edge fibre optic system is revolutionising fire protection, offering swift detection and prevention across entire solar farms and associated High Voltage.
Data Centres are prone to bus duct failures, which can lead to unplanned downtime. Preventing the loss of important data and confidential assets is achievable with early detection fire safety technology.
Experience advanced linear heat detection with APSensing’s N45-Series. Elevate safety in industrial settings with precision fire monitoring.
Traditional fire detection methods, the safety risks they pose in hazardous environments, and how fibre optic technology is revolutionising the industry.
When it comes to mine safety, combustion can cause serious damage to personnel and assets in a mine. Our solution pinpoints these risks.
Conventional fire detection systems are onerous in many ways: device intensive, require costly maintenance and time consuming replacements. All these aspects cause a burden for
A report from Queensland Resources Safety and Health recommends that resources companies “Implement a computerised incident management system“
Data Centres demand a high power consumption in daily operations, requiring bus ducts for electricity distribution.
Embracing innovation is logical when it offers a superior approach. Traditional fire detection methods often fail, require frequent maintenance, and lack early detection capabilities.
Fibre optic Distributed Temperature Sensing (DTS) is transforming fire detection in Australian industries.
This technology provides precise, tailored solutions to common fire risks without maintenance, or downtime. Our system has a lower total cost of ownership over the lifespan of the assets it’s protecting. I would there change the “added costs” with this statement.
Fibre optic fire solutions may appear complex at first glance. But, our experts are here to guide you as you explore the potential of our fire detection system. We have even compiled some frequently asked questions to get you started.
Advanced Photonics Australia brings practical engineering expertise and innovative technology to the forefront. Harnessing cutting-edge photonics technology, we tackle each unique challenge head-on using Distributed Temperature Sensing (DTS).
© Copyright 2023 Advanced Photonics Australia
Website developed by The Marketing GP
Legalities